Curt, Shruthi, Vedant
Project Sentence
Home Automation
Smart glove that helps the user control their TV and smart switches/lights using hand gestures
Taltos-oid (SRF)
Human augmentation device providing users with an extra thumb for everyday tasks.
Weekly Accomplishments
Curt –
[Note for showcase: I will need power for my laptop / backup for SRF power supply]
First major accomplishment this last week was putting in the time to construct the flex sensors for the glove. My current status with this task is that all of the flex sensors are constructed, tested, and sewn onto the glove.

Pinky and ring finger lower flex sensors are completely sewn and have been tested with my Analog Discovery for a valid flex signal.
I then moved onto sewing the conductive thread to connect the flex sensors to wires that will lead to the microcontroller. After several approaches / experiments I found a relatively simple solution to interface between wires (with female headers) and the conductive fabric. My current status is the first one has been sewn on and tested. I plan on completing the rest of these this week by end of day Wednesday.
On a seperate thread of work I have worked on the firmware for the SRF. Currently I am debugging the firmware as I continue physical development efforts. Additionally, I have experimented with the Adaboost random forest approach to determine joint states. I need to write a program that runs on my laptop that communicates to the firmware level that I have written. To that end, I did define and implement a JSON interface in the firmware.
Finally, on Thursday last week I received my final shipment of parts which included the fourth servo needed to rework the finger. After reworking the design several times (as documented in the pictures below) I came up with a solution that works mechanically.

Added rotation joint at bottom. Finger collides with hand when rotating. Also the finger movement is restricted as it sits in a uncomfortable spot in space around hand.

Rotation joint in middle, this allows better movement in 3D space but rotation joint is too close to hand causing collision with the protrusions from the finger.
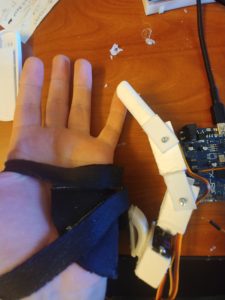
Changing the angle that the finger sits at to prevent rotation collisions and make it feel more natural in the space around the hand. Problem is this is a larger finger / extends from hand further.

Also the piece I built is out of broken 3D printed hinges, copious hot glue, and part of a command hook taken from my wall. Looks fine several feet away but not as aesthetically pleasing close up.
There are several issues with this final version of the robotic finger. Namely, the grip torque is further reduced, size/bulk increased, and abundance of hot glue. While I acknowledge these issues as failures of the current design, it should nonetheless inform future iterations.
Remaining Tasks
- Construct wire to conductive thread adapters (4x)
- Sew on conductive thread adapters
- Debug / verify correct operation of flex sensor circuit
- Build microcontroller wrist-strap with velcro
- Build microcontroller board using solder protoboard
- Debug / verify correct operation of firmware for both finger and glove
- Write PC program for controlling finger joint states from flex data. Requires collecting and training ML data
- [Optionally] Get either Bluetooth serial or WiFi websocket for wireless operation
- Poster design and language complete
Shruthi –
This week we spent time on discussing and developing ideas for the poster and its contents. I made an initial draft and working towards improving it. We also made a few more fabric flex sensors and sewed them on. Also planned the layout of where the circuitry goes into. The idea is to have no cross overs or short circuits. Another challenge we seem to run into is to try and figure out the best way to power the particle photon. We could use a power bank, however we aren’t sure how it has bearings on the overall user experience and the portability factor. We may also consider sewing on a Li-Po battery to Vin of the photon. We also had a discussion with Kevin on how to best demo the functionality. I am looking at pulling the browser data from particle website either using a browser emulator or java-script and working towards building a local server to do this. Here is a photograph of the sewed on flex sensors.
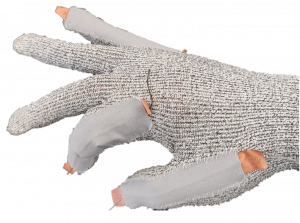
Vedant –
This week we worked on sewing the fabric DIY sensors onto the glove, the poster, and well as finalizing the code for the IR transmitter. I was able to understand how to convert the IR Hex Codes I had to Raw Codes, which is then used in a pulse and delay combo in a for loop that loops over the Raw IR codes list. I was able to get the IR connected to the photon to emit IR signals turn on/off my TV and increase volume.
Material List
Home Assistant Sub-Project
- Particle Photon – $19.00 (1)
- Flex sensor – 4.5 inches – $12.95 (1)
- Flex sensor – 2.5 inches – $7.95 (1)
- IR LEDs
*We decided to go ahead with more of the DIY flex sensors. So we might possibly need more velostat and copper sheets and conducting thread.
SRF Sub-Project
Already purchased / owned
- Glove for prototype [final version subject to change based on prototype]
- Sparkfun IMU – $14.95 (1)
- Flex Sensor – 4.5 inches – $15.95 (1)
- ESP32 Dev Board – $15.00 (1)
- High Torque Micro Servo – $9.95 (3)
- Resistive Force Sensor – $7.00 (1)
- Flex sensor – 4.5 inches – $12.95 (1)
- 3D printed SRF – ~$14.00 (N/A)
- Glove [Final design] – $14.99 (1 ordered)
- PCBs – N/A (N/A ordered)
- High Torque Micro Servo – $9.95 (1)
- 3.3V to 5.0V Level Shifter IC – ~$1.00 ( 1)
- I2C Servo Driver Board [in case issue with microcontroller persists] – $14.95 (1)
Need to Purchase / Being Shipped
- Resistive Force Sensor – $7.00 (5)
- Flex sensor – 4.5 inches – $12.95 (3) and/or Flex Sensor 2.5 inches – $7.95 (8)
Areas of Concern
Curt –
Primary concern for this week is finishing the sewing of conductive thread on the glove, wiring the microcontroller with all components, and writing/debugging the software for the project. There is plenty of work to do and not much time.
Secondary concern is the poster which I will probably have time to work on Tuesday evening / night. Again not much time to complete these items.
Shruthi –
A few areas of concern at this stage is to how to best integrate the circuit and battery into the fabric keeping in mind its aesthetic and portability requirements
Vedant –
Areas of concern as of now include getting the code for the flex sensor integrated with the IR emitter and making sure we are able to sew the circuit onto the glove in time.